Group Members
Postdoctoral Researchers
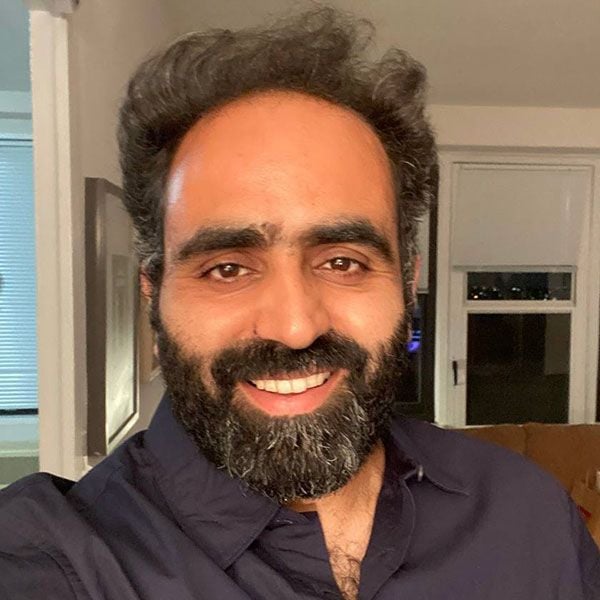
Tawqeer Nasir Tak
Ph.D.: IIT Bombay, India
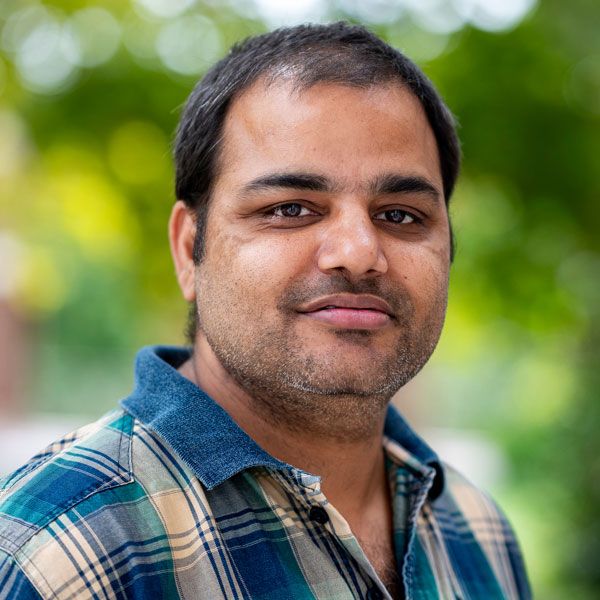
Aalok Jha
Ph.D.: IIT Kanpur, India
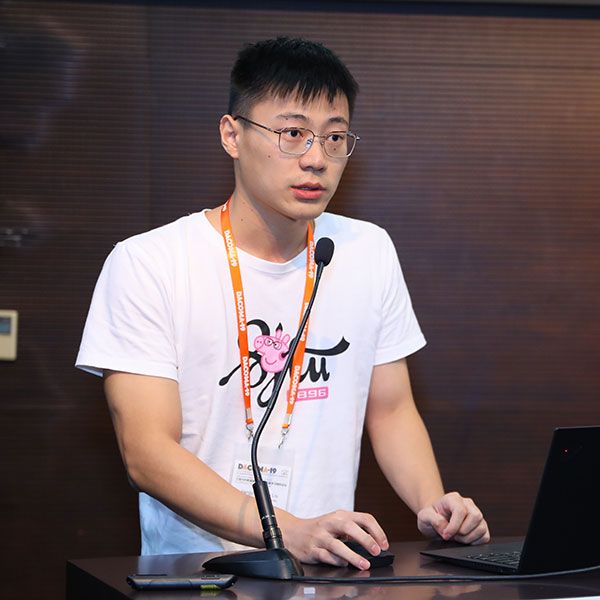
Yangyuanchen Liu
Ph.D.: Duke University
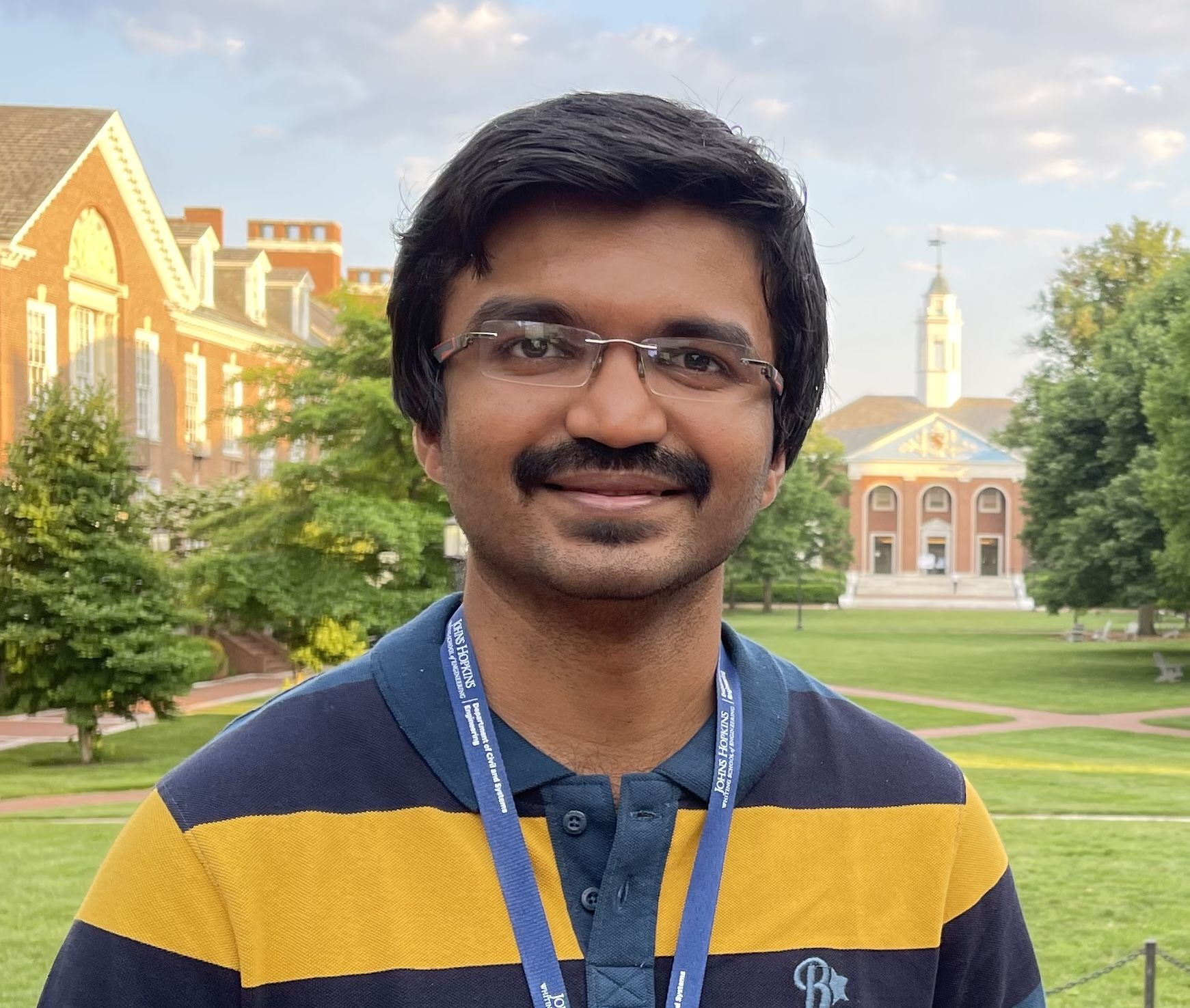
Prajwal Kammardi Arunachala
Ph.D.: Stanford University (Sept ’24)
M.S.: Stanford University (Apr ’19)
B.Tech.: Indian Institute of Technology Bombay (May ’17)
Improving existing phase field fracture models for Ti-alloys, extending them to account for fatigue loading, and ensuring effective parametric upscaling for large-scale industrial applications.
Sponsored by Office of Naval Research
Current Ph.D. Students
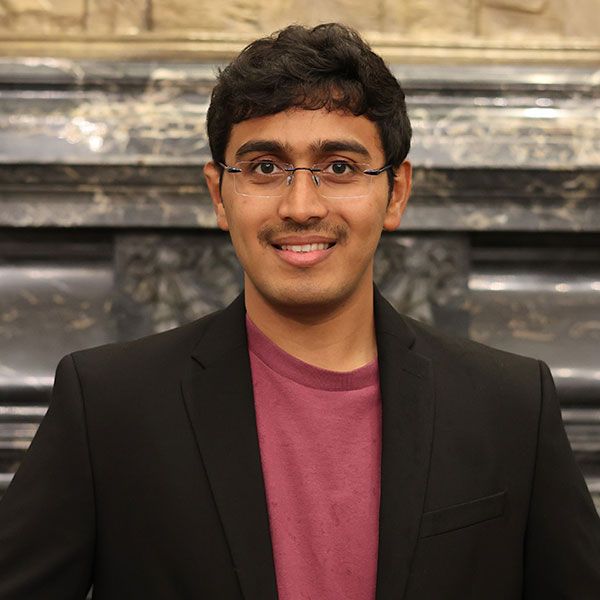
S.K. Gargeya
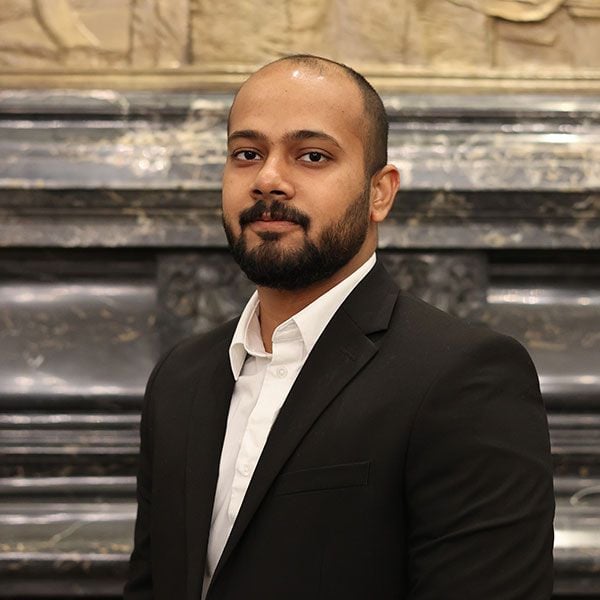
Kishore Nair
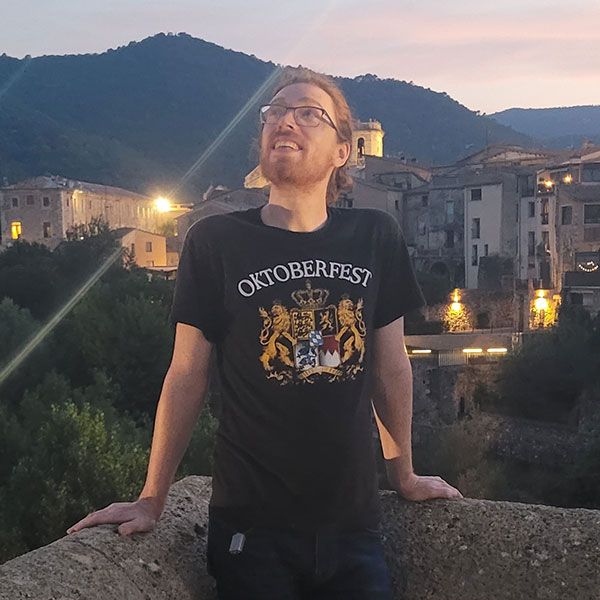
Joshua Stickel
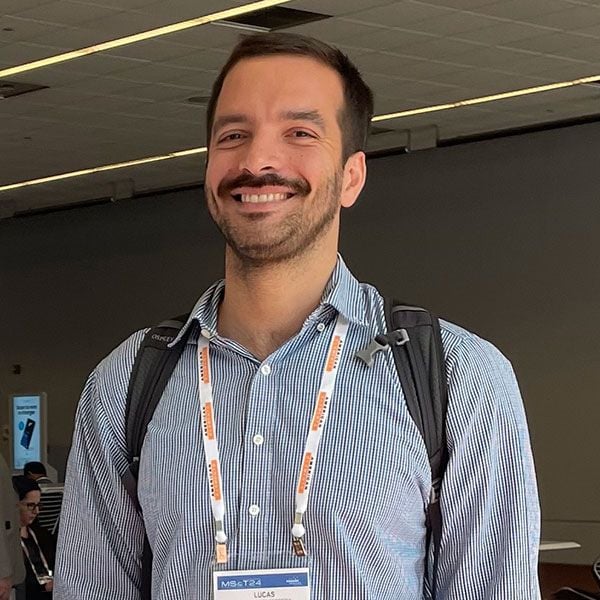
Lucas Ferreira
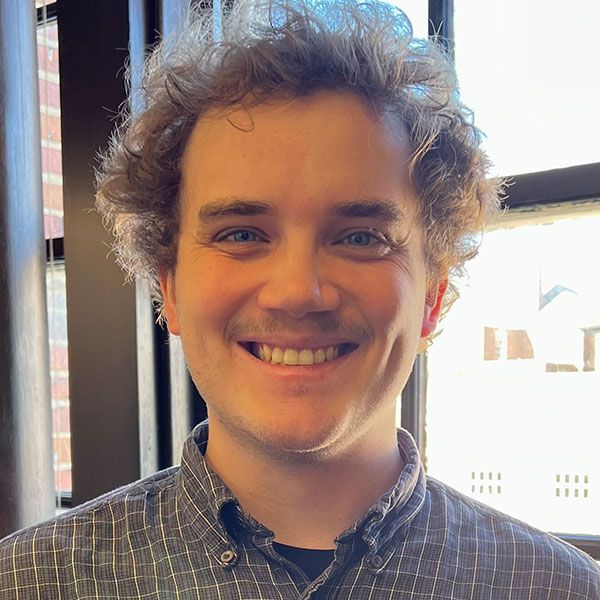
Nolan Strauss
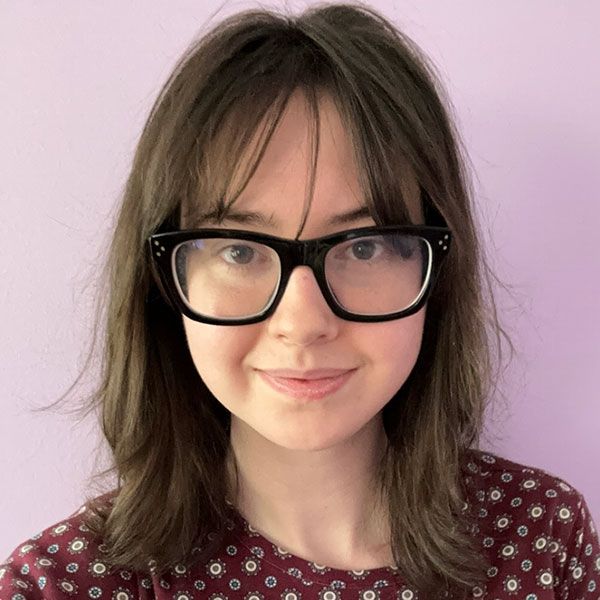
Isabella Snyder
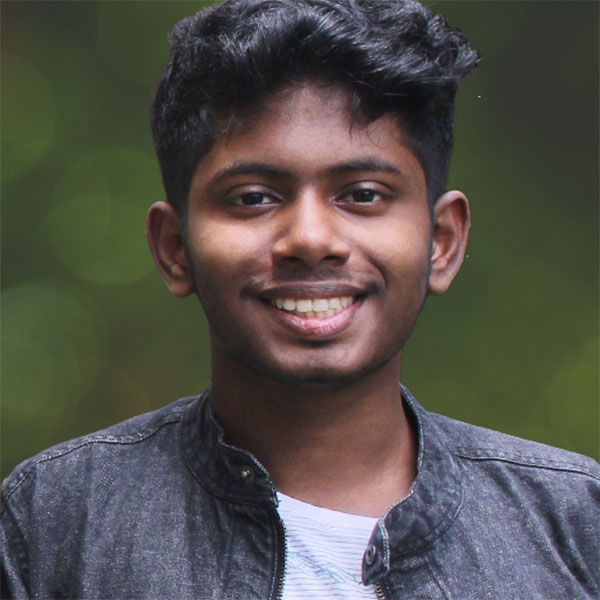
Gino Varkey
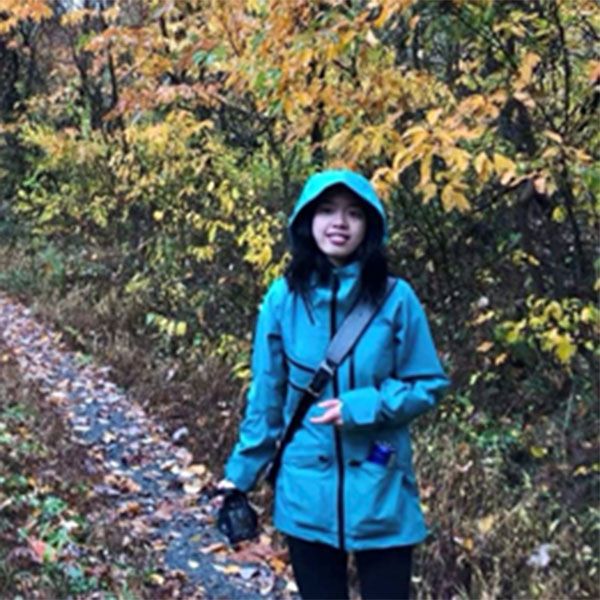